From spreadsheets to intelligent planning
Set up in days, customized in weeks.
Planning teams and leaders' perspectives
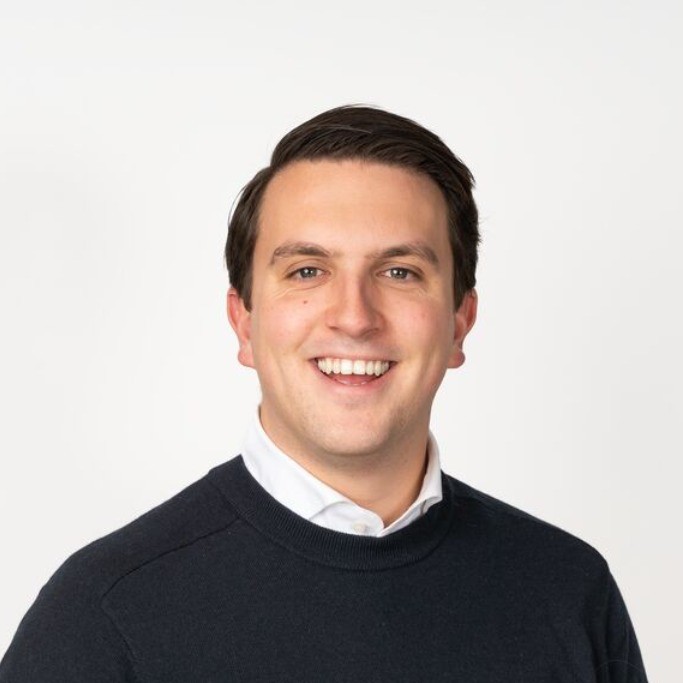
"Impressed by the knowledge and fast results of Horizon. Together we turned plans into action in no time."
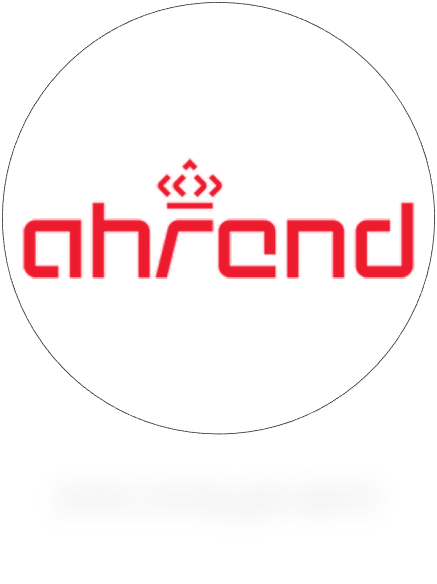
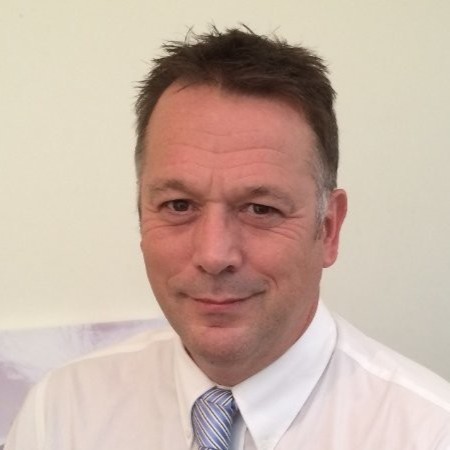
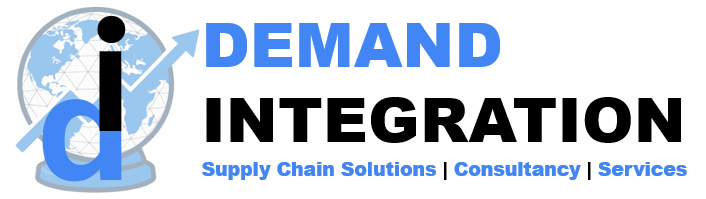
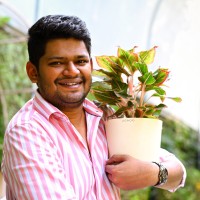
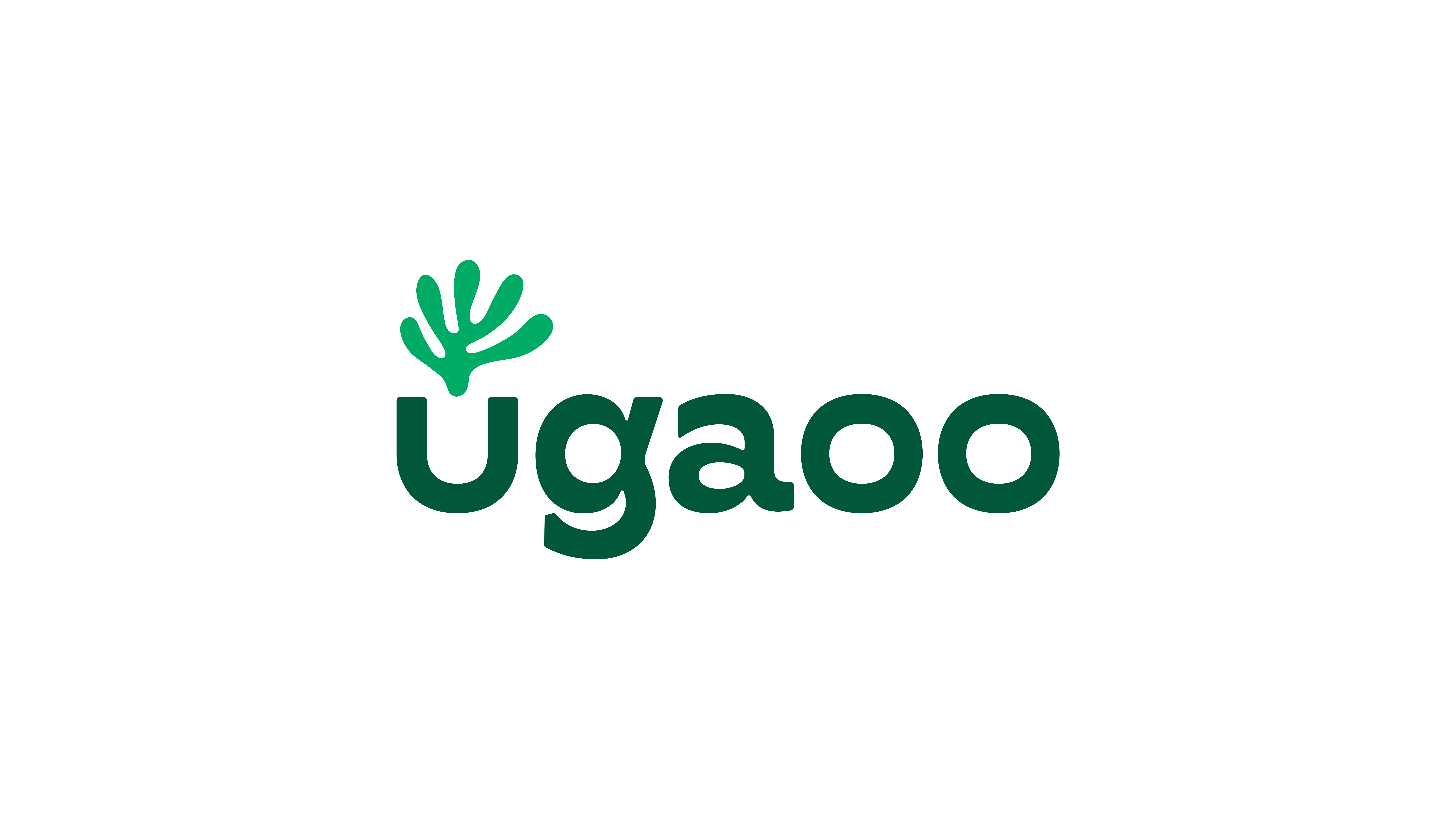
Our Partners
We work with these partners in the Benelux, Australian, Indian, and UK regions.
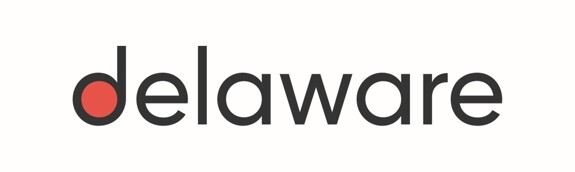
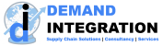
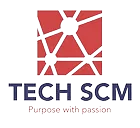
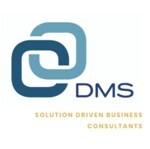
Discover the Demand Scan
Immediate insights into the performance of demand planning models for your business, the maturity of your organization, and demand characteristics.
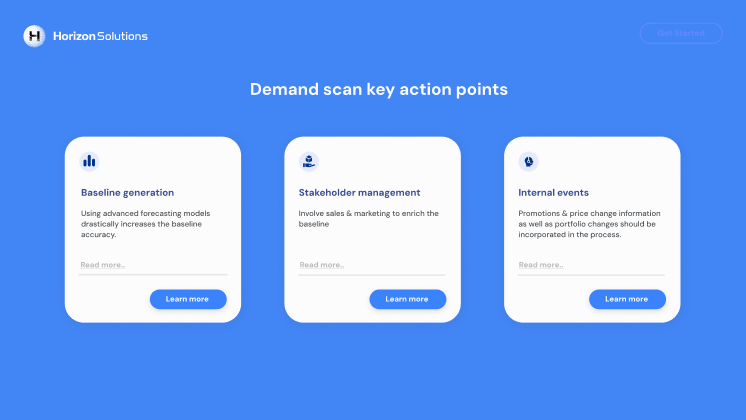
Webinar on August 14th
From Excel to an intelligent planning platform in weeks.
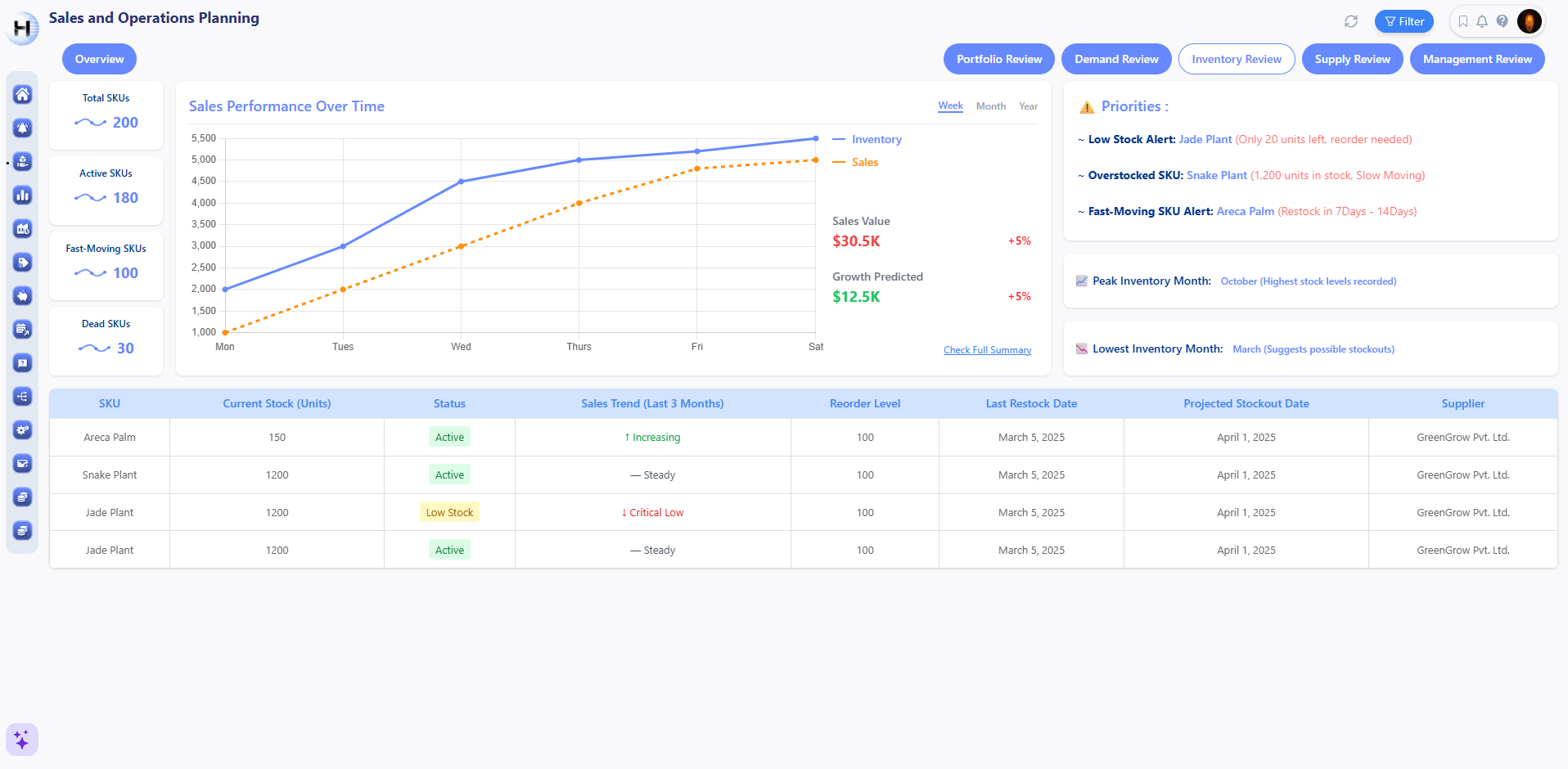
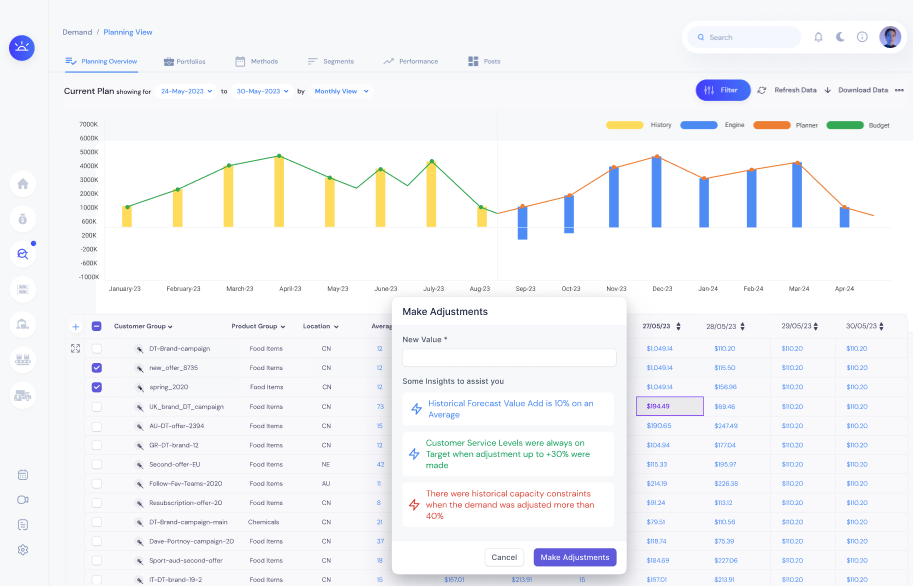
Self Learning
Through Automated Best Model Selection via Machine Learning, Horizon detects at which level of the product-customer-location hierarchy patterns exist and which blend of models best fit that pattern
Get insight into which model is used and why: full transparency
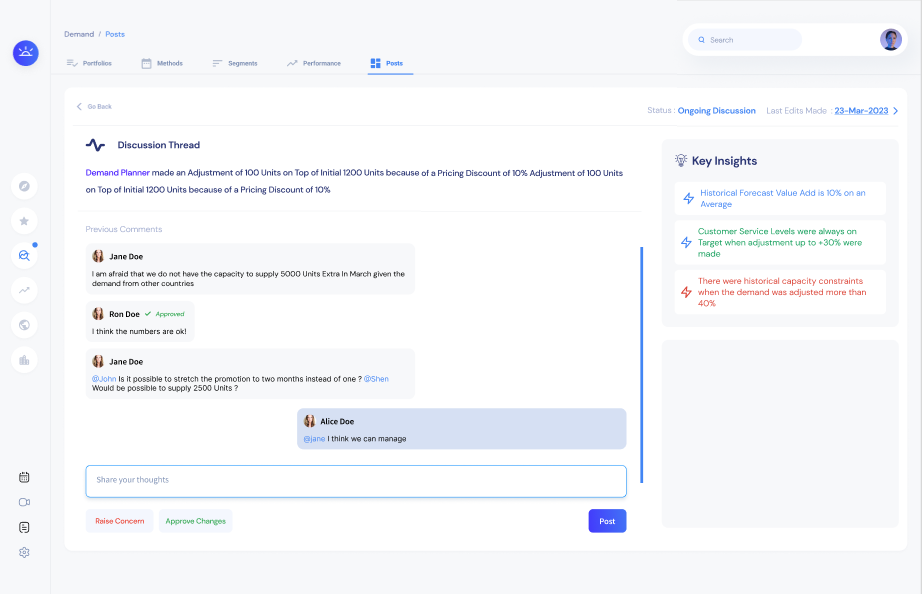
Continuous and Direct Collaboration
Get rid of monthly S&OP meetings to review changes
Keep track directly of proposed adjustments, accept them or add comments
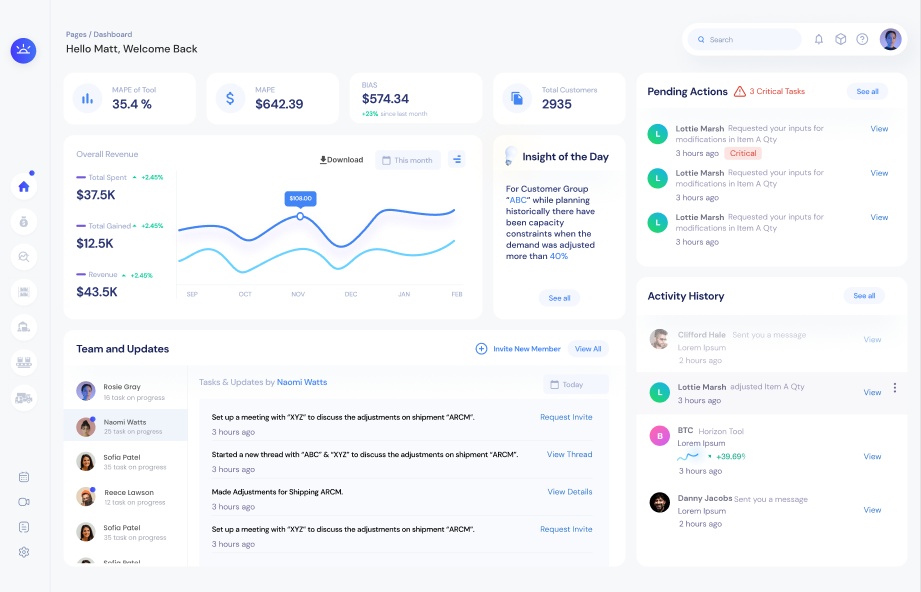
Simplified Product Lifecycle Management
An easy way to manage phase-in, phase-out, or new product introductions
Horizon proposes which customer is most likely to buy a new product and proposes launch quantities for new products
Smart planning
Adjustments and immediate impact across supply chain, finance, and sales
Horizon connects sales forecasts, budgets by finance, and supply chain forecasts.
Changes are translated into production plans dynamically so that different decisions can be evaluated.
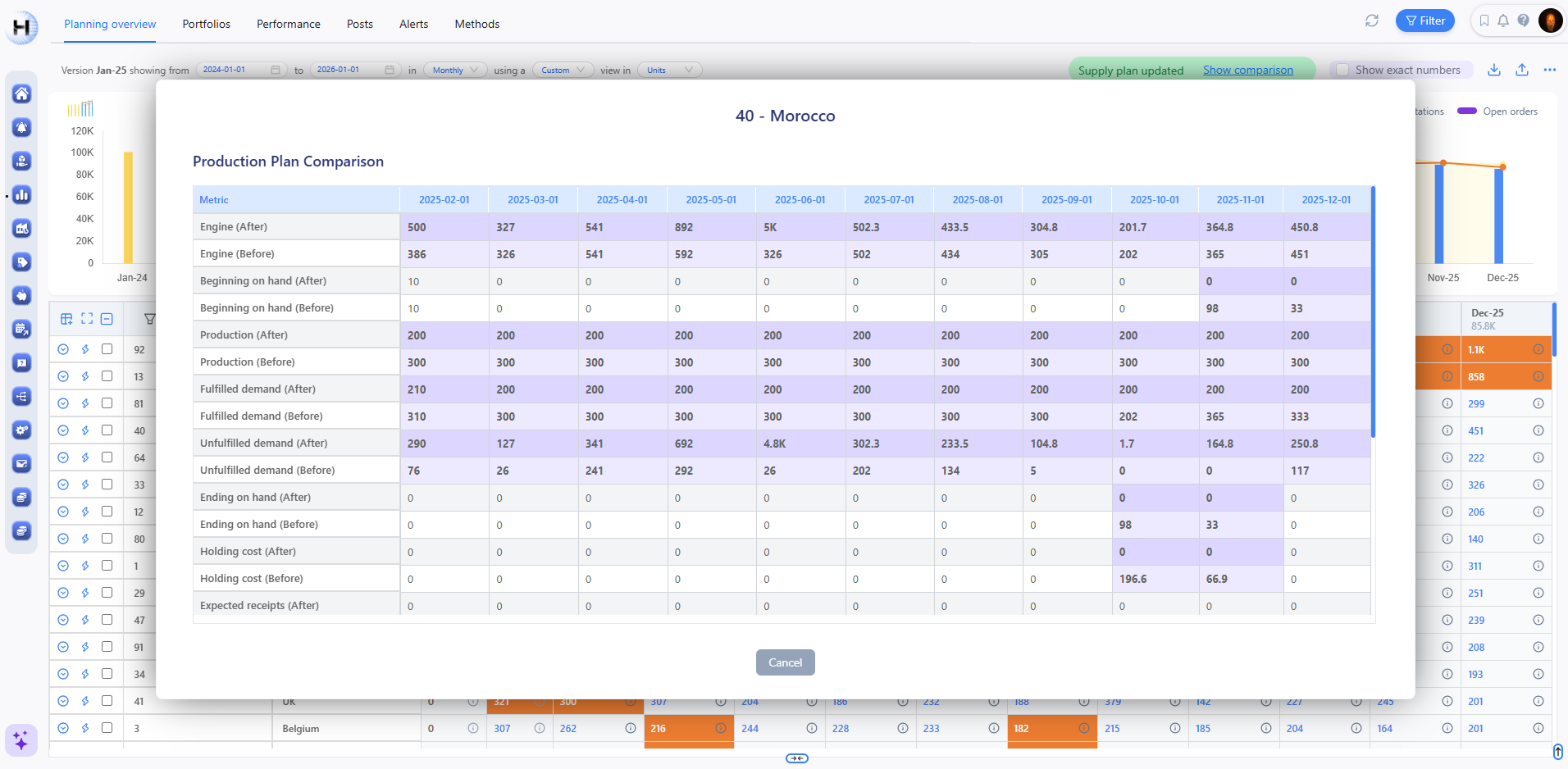
Highlighting what matters while you stay in control
Horizon learns from your workflow, comments, and tasks, adapting to how you plan.
It suggests focus areas, highlights relevant background info when making an adjustment, and helps teams collaborate in real-time.
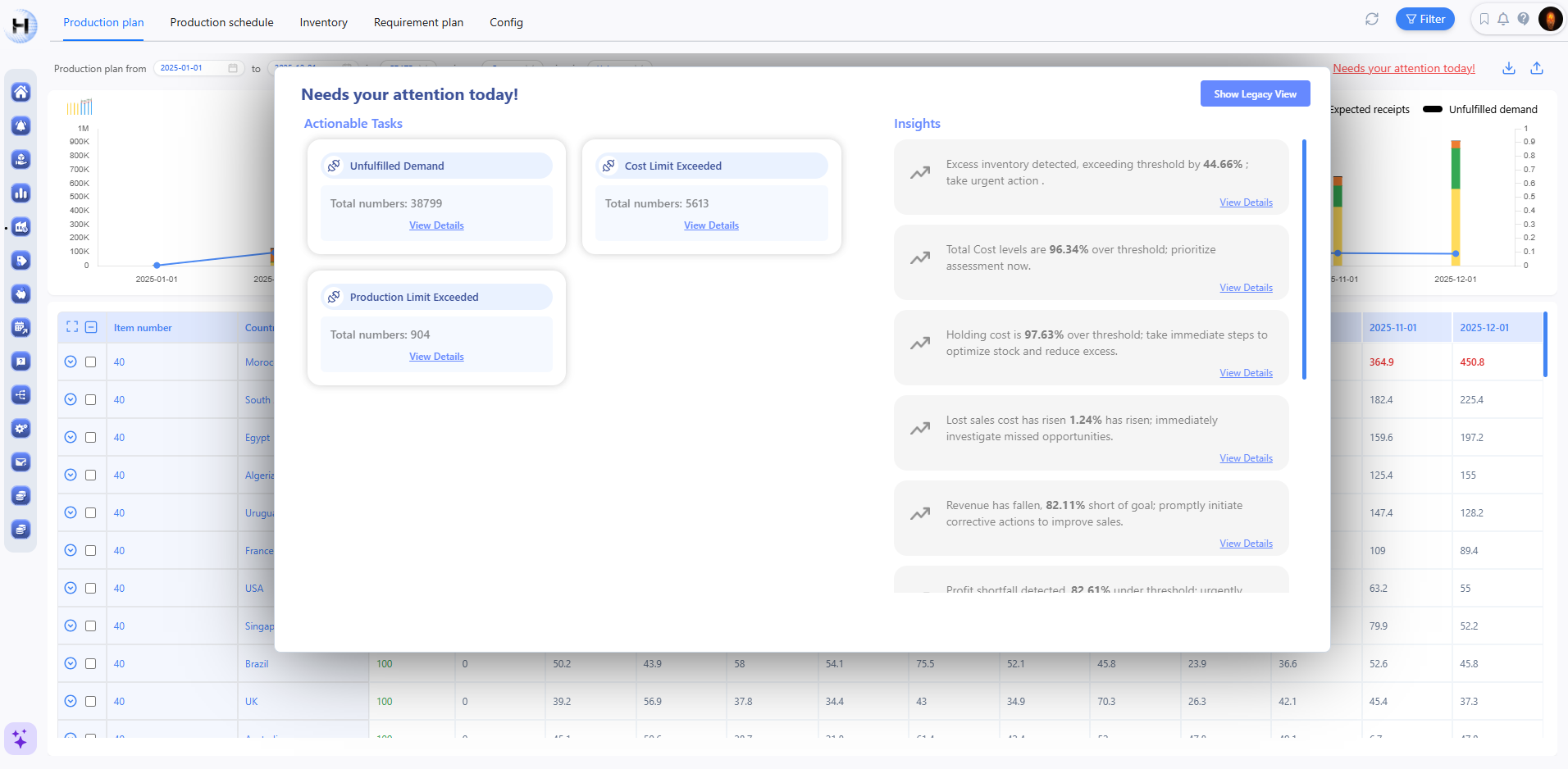
Dynamic model selection and optimization across demand, inventory, and supply
Horizon selects the best statistical or machine learning model for demand forecasting for each product category.
It adapts the inventory strategy based on demand variability and lead times and optimizes the production plan based on real-time constraints.
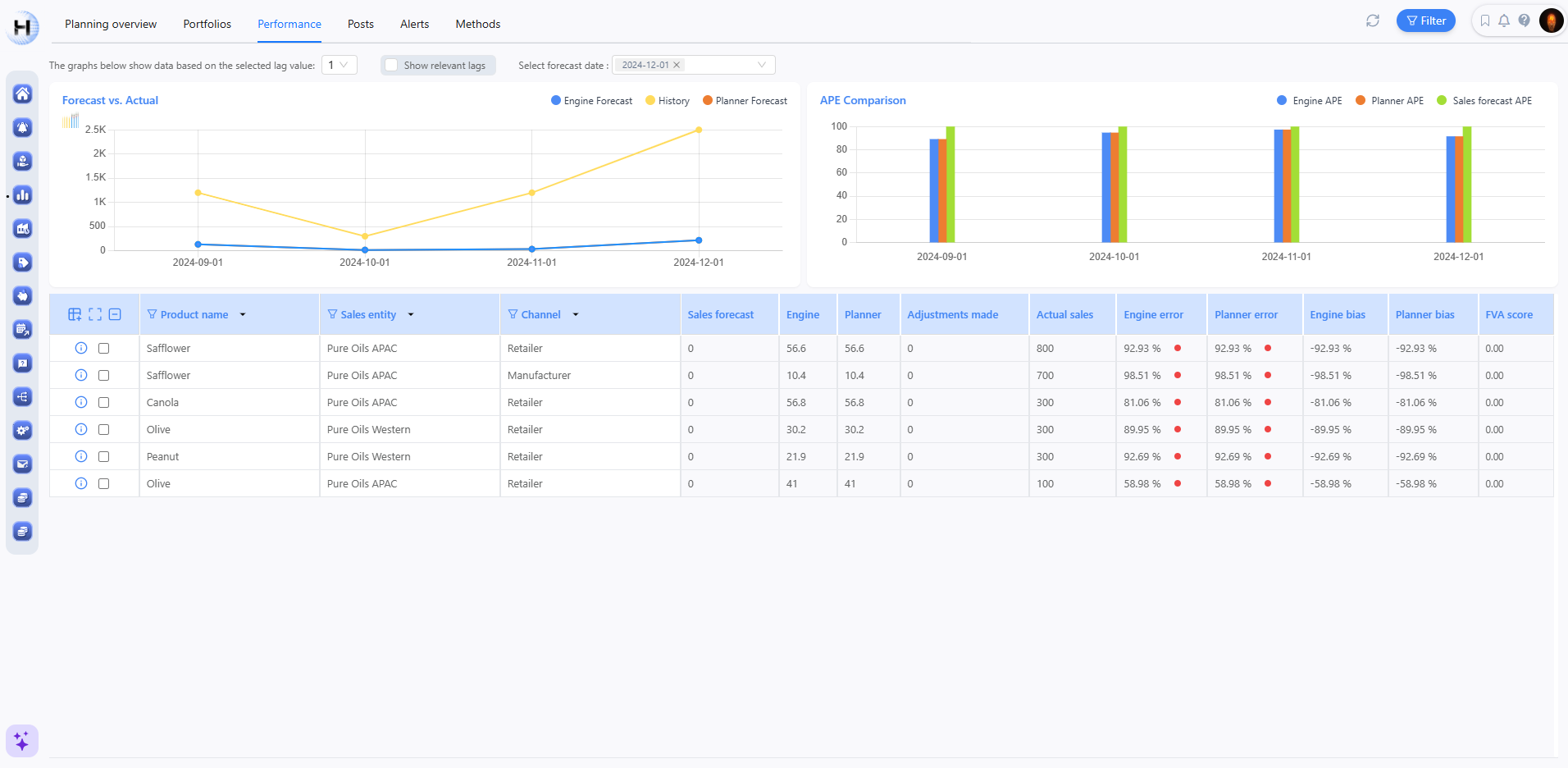
Insights for clearer planning
Planning Lens
FAQs
-
What are the benefits for planners?
Supply chain planning tools help planners save time, reduce errors, and improve decision-making by automating calculations and providing a structured planning process:
-
Time savings: automated calculations and structured workflows eliminate manual effort
-
Fewer errors: cloud-based, real-time updates ensure accuracy, and all changes are tracked
-
Improved focus: AI-guided suggestions highlight priorities, helping planners stay on track
-
Collaboration & visibility: integrated with ERP and other planning tools, reducing the need for manual reporting and presentations.
-
-
What are the benefits for the company?
A well-implemented supply chain planning solution doesn’t just support planners but drives company results:
-
Better decisions: mathematical models enhance demand forecasting, supply planning, and inventory management.
-
Optimized working capital: reduces excess inventory while preventing stockouts.
-
Lower lost sales: more accurate demand planning ensures products are available when needed.
-
Efficiency gains: less time spent on spreadsheets and manual processes means teams can focus on strategy.
-
-
Which are the key trends in supply chain planning?
Modern supply chain planning is evolving, with AI and machine learning playing a growing role. Some of the biggest trends include:
-
Machine learning in demand planning: improves forecast accuracy by detecting trends, outliers, and external drivers
-
Supply optimization is still driven by mathematical models: linear and mixed-integer programming (MIP) remain the core methods for production and inventory planning
-
AI-assisted planning: large language models help planners prioritize tasks, track changes, and measure forecast value add (FVA) but do not replace optimization models
-
End-to-end scenario planning: real-time adjustments allow businesses to test different demand, supply, and financial scenarios instantly
-
-
What is the difference with an ERP system?
ERP systems are systems of record, designed to track past transactions, inventory levels, and financials. However, they lack the analytical capabilities needed for advanced planning.
A supply chain planning tool works on top of an ERP, providing:
-
Advanced forecasting and supply planning optimization: statistical models, machine learning, and supply chain solvers that ERP systems lack.
-
Scenario planning: enables planners to test different demand and supply situations dynamically.
-
Real-time collaboration: cloud-based planning improves visibility across departments and automates updates.
-
-
What is Horizon?
Horizon is an advanced planning platform that helps businesses optimize their supply chain decisions:
-
End-to-end planning: covers demand planning, inventory management, production planning & scheduling, and IBP.
-
AI-driven: Horizon highlights priorities, tracks planner adjustments, and measures forecast accuracy.
-
Supply optimization: uses linear programming (LP) and mixed-integer programming (MIP) for supply chain optimization, depending on the exact business constraints & requirements.
-
Customizable & fast to deploy: no lengthy onboarding or setup: Horizon is up and running in days.
-
Built by experts: created by a team with experience at Logility, O9 Solutions, and E2open, recognizing the gap in the market between Excel-based planning and legacy solutions.
Horizon provides low-risk, high-impact planning that integrates with your ERP.
-